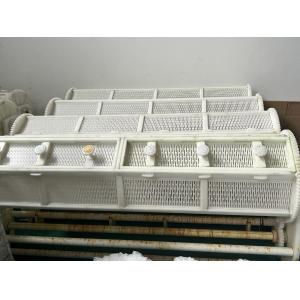
Add to Cart
1. Technological process of production(Taking nickel barrel plating as an example)
feeding→alkaline degreasing→electrolytic degreasing→water rinsing→pickling→water rinsing→nickel pre-plating→water rinsing→nickel plating→water rinsing→hot water rinsing→drying→protection→drying→put down
2. Solution preparation
Nickel plating solution: NiSO4.6H2O 100±20 g/L
NiCl2.6H2O 100±20 g/L
H3BO3 40±10 g/L
Wetting agent 10±2 ml/L
Brightening agent 1.5 ml/L
PH 3.8~4.6
Temperature 55±5 ℃
Anode material electrolytic nickel
3. Maintenance and adjustment of nickel plating solution
3.1 It is necessary to regularly ensure the normal dissolution and good conductivity of the anode.
3.2 Regularly analyze the solution and adjust it in a timely manner.
3.3 Strictly control the pH value of the solution.
3.4 Add additives at a rate of 170ml/KAH.
4.The causes and troubleshooting methods of common faults
Common faults | Cause of occurrence | Solution |
Pitting on the coating | Organic impurities in the plating solution | Adsorption with activated carbon |
Lack of wetting agent | Add wetting agent 0.5-1ml/l | |
High or low pH value | Adjust PH to specification with dilute sulfuric acid or dilute sodium hydroxide solution | |
Iron impurities in the plating solution | Plating solution treatment | |
Bright coating with local matte (foggy) | Copper impurities in the plating solution | Removing Copper Impurities by Electrolysis |
Insufficient brightener | Adding brightener | |
The coating has dark or black stripes | Organic impurities in the plating solution | Plating solution treatment |
Zinc impurities in the plating solution | Removing Zinc Impurities by Electrolysis |
5. Major treatment methods for plating solution
5.1 Acidification: Adjust the plating solution with sulfuric acid to pH=3 and heat it up to around 50 ℃.
5.2 Oxidation: Add 2-3 ml/l of 30% hydrogen peroxide under continuous stirring for 2-3 hours.
5.3 Alkalization: adjust PH=5.5~6.2 with dilute sodium hydroxide solution.
5.4 Activated carbon treatment: Slowly add 3-5 g/l of powdered activated carbon under continuous stirring, heat to 60-80 ℃, continue stirring for a period of time, and then let it stand for filtration.
6. Removal of Unqualified Nickel Layer
6.1 Chemical Removal of Nickel Coatings on Copper and Copper Alloys
Anti pollution salt (sodium m-nitrobenzenesulfonate) industrial grade 70 ± 10 g/l
Sulfuric acid (H2SO4 specific gravity=1.84) industrial grade 70 ± 10 g/l
Sodium thiocyanate (NaSCN) 0.5 ± 0.3 g/l
Temperature 90 ± 10 ℃
Time surface changes from black to brown
Brown film is removed in the following solution
Sodium cyanide (NaCN) industrial grade 35 ± 5 g/l
Sodium hydroxide (NaOH) industrial grade 35 ± 5 g/l
Temperature room temperature
Time until net removal
7. Packaging & Shipping
We can pack it by pallet, or according to the customers' specific requirements.
Port: Shanghai/Ningbo
8. Our Services
In order to guarantee the customers are able fully to operate the machine, if the customer need, we can help customer training, includes:
(1) Correct operating mode
(2) Correct maintenance way
(3) Correct technological process control
(4) Remove simple problem
All the electroplating machine of our company have already been widely used in electroplating area.
Any doubt please contact us.